KingKa: Tailor-made efficient cooling solutions for customers
As a leading heat sink supplier, KingKa is committed to providing customers with efficient and reliable cooling solutions. The following is the complete service process and case of customizing Heat Sinks for a customer, demonstrating our professional capabilities and customer-first service concept.
Customer Requirements Overview
The customer needs a Heat Sink system that meets the following design requirements:
TEC parameters: 12.1V/12.4A/Qcmax 86.5W × 4 pcs
Total thermal power: 155.7W × 4 = 622.8W
Material selection: Use C1100 copper to make the heat sink
Manufacturing process: Use skived fin process and heat pipe welding, and need to configure 10 heat pipes with a diameter of 6.35mm
Fan configuration: Install 2 6025 fans, each fan provides 49.4 CFM air volume
Environmental conditions: Ambient temperature is 25℃, operating under natural convection, working pressure is 101325N/m², and thermal radiation is not considered.
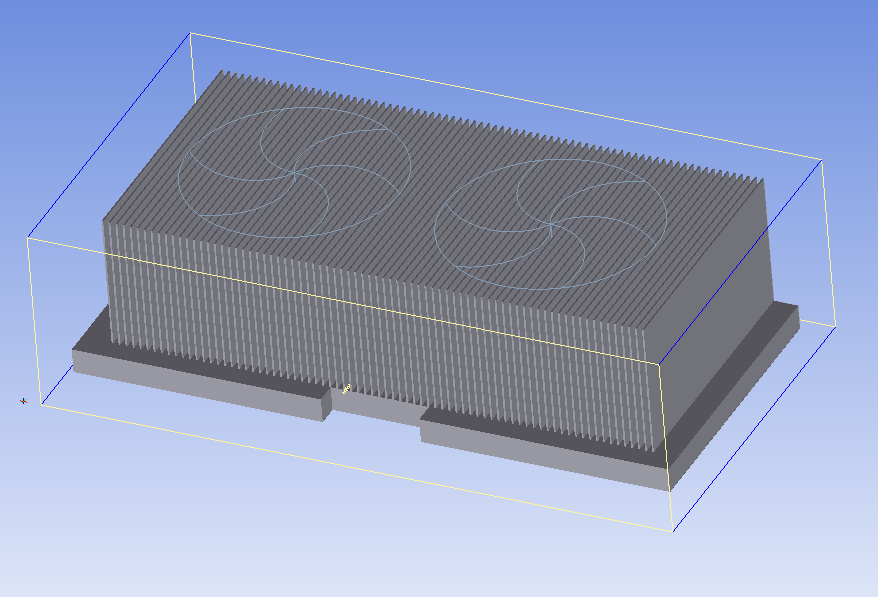
Design and simulation tools
We applied a variety of design and simulation tools in the project to ensure that the final product meets the performance requirements:
Ansys 22.0
Used to simulate thermal management solutions and optimize heat sink structural design.
Pro/E
Perform accurate 3D modeling and quickly generate heat sink prototypes that meet actual applications.
Simulation and parameter setting
To ensure the accuracy of the simulation results, we completed the analysis based on the following parameters:
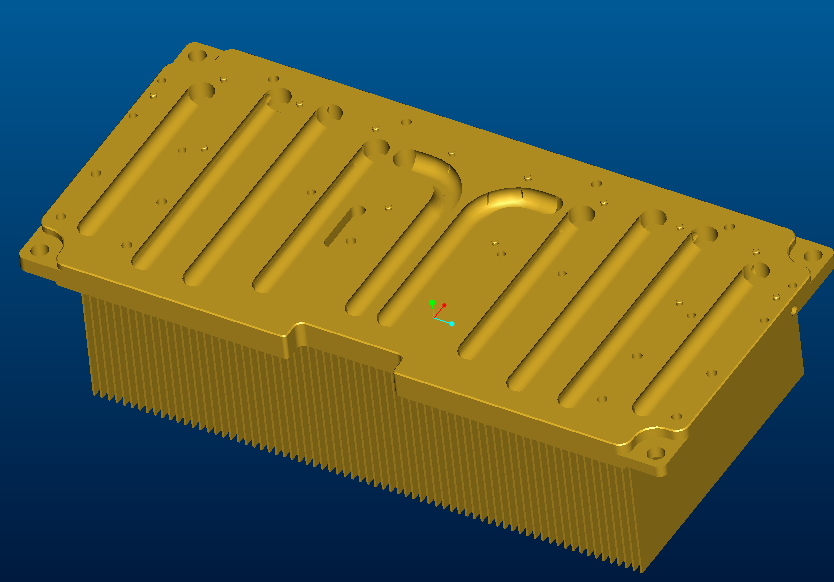
Basic parameter settings
Ambient temperature: 25℃
Heat radiation: not considered
Flow mode: turbulent
Working pressure: 101325 N/m² (natural convection)
Meshing
Number of meshes: 1,043,370
Mesh parameters:
Single mesh parameter setting
Independent mesh assembly
Support multi-level meshing
Allow minimum gap changes
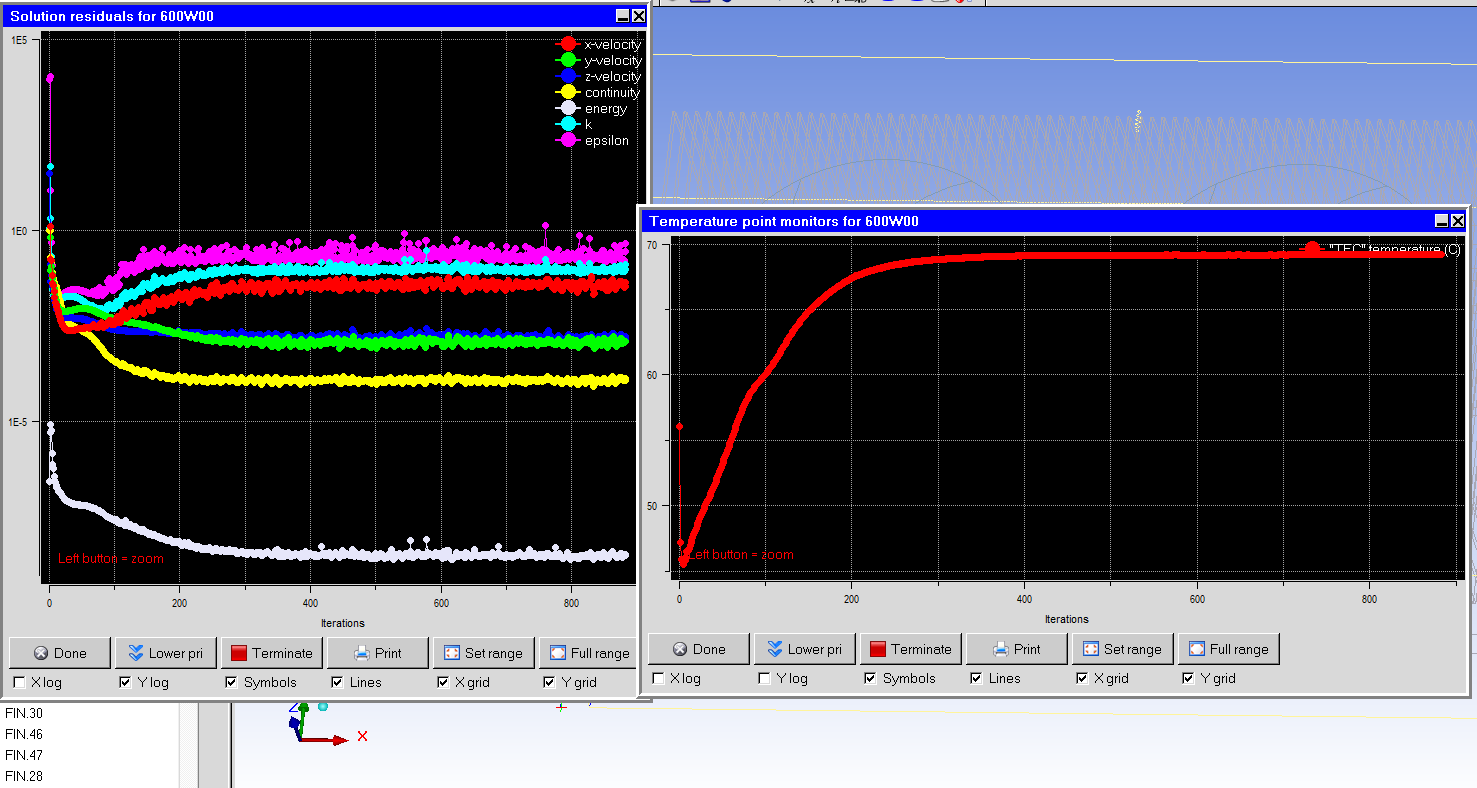
Simulation results
Under the assumptions based on a simple model, we obtained the following results:
TEC surface temperature
Average: 75.4℃
Heat sink maximum surface temperature
Average: 54.3℃
Although the simulation results are slightly biased, it provides direction and basis for optimizing the design.
Manufacturing and testing
After design verification, KingKa began to manufacture the heat sink. The whole process includes the following steps:
Material selection and processing
The heat sink is made of C1100 copper with high thermal conductivity. The fin cutting process ensures uniform fin spacing and thickness to improve heat conduction efficiency.
Heat pipe welding
Using a precise welding process, 10 heat pipes with a diameter of 6.35mm are firmly embedded in the heat sink to enhance thermal conductivity.
Fan installation
Equipped with 2 6025 fans, each fan provides 49.4CFM airflow, effectively supporting the overall heat dissipation performance of the heat sink.
Customer feedback and actual application
After the product was delivered, the customer conducted actual testing on the performance of the heat sink and found the following highlights:
Efficient heat dissipation
The average temperature of the heat sink was consistent with expectations, ensuring the stable operation of the TEC system.
Stability and reliability
Even under high-power working conditions, the heat pipe and fan work together to keep the cooling system with superior performance stability.
Precise service
The customized service and detailed technical support provided by KingKa have won high recognition from customers.
This project fully demonstrated KingKa's professional capabilities in the field of heat sink design and manufacturing. From demand analysis, design simulation to manufacturing delivery, we always focus on customer needs and provide customers with the best solutions through advanced technology and high-quality materials. In the future, KingKa will continue to help more customers succeed with professional services and high-quality products.
KingKa - Make thermal management easier!
If you have any heat sink needs, please feel free to contact us, KingKa will serve you wholeheartedly!