heat sinks are critical components in the semiconductor industry, playing a vital role in managing thermal performance and ensuring the reliability of electronic devices. As semiconductor devices continue to shrink in size while increasing in power density, effective thermal management has become a cornerstone of modern electronics design. This article explores the technologies behind Heat Sinks, their applications in the semiconductor industry, and future trends in this field.
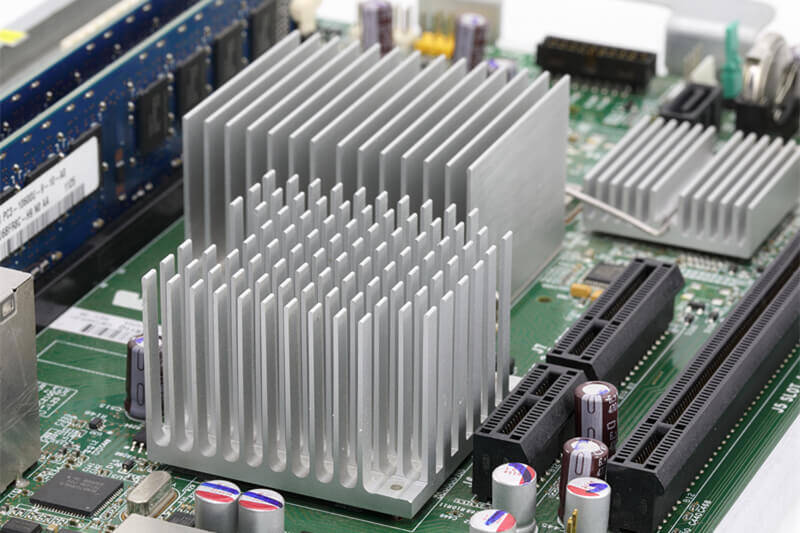
Heat Sink Technology and Applications
1. Process Technology Overview
Heat sinks are designed to dissipate heat from a solid surface, primarily through conduction and convection. They are typically constructed from high-thermal-conductivity materials such as aluminum, copper, or a combination of both. Manufacturing processes include extrusion, die-casting, machining, and more recently, additive manufacturing for complex geometries. Surface treatments like anodizing or plating enhance corrosion resistance and heat transfer efficiency.
1.1 General points
In order to provide optimum performance of semi-conducting devices it is essential not to exceed the maximum junction temperature indicated by the manufacturer.
Generally this maximum junction temperature can only be maintained without exceeding it by running the device concerned at lower power outputs.
At outputs approaching the maximum ratings semi-conductor devices have to be cooled by so called heatsinks..
The thermal performance of these heatsinks primarily depends on the thermal conductivity of the material from which they are made, size of surface area and mass.
In addition, surface colour, mounting position,temperature, ambient air velocity and mounting place all have varying influence on the final performance of the heatsink from one application to another..
There are no agreed international standard methods for testing electronic cooling systems or for the determination of the thermal resistance.
1.2. The determination of thermal resistance
The thermal resistance is the parameter that is the most important in cooler selection, apart from mechanical considerations. For determination of the thermal resistance the following equation applies:
Equation 1: RthK =
− ( RthG + RthM ) =
− RthGM
In case of an application where the maximum junction temperature is not exceeded the temperature has to be verified.
When the case temperature has been measured the use of the following equation will enable the maximum junction temperature to be calculated:
Equation 2: ϑi = ϑG + P x RthG
The meaning of the determinants:
ϑi = maximum junction temperature in °C of the device as indicated by manufacturer. As a »safety factor« this should be reduced by 20-30 °C.
ϑu = ambient temperature in °C.
The rise in temperature caused by radiant heat of the heatsink should be increased by a margin of 10-30°C.
Δϑ = difference between maximum junction temperature and ambient temperature.
ϑG = measured temperature of device case (equation 2).
P = maximum power rating of device in [W] Rth = thermal resistance in [K/W]
RthG = internal thermal resistance of semiconductor device (as indicated by manufacturer)
RthM = thermal resistance of mounting surface. For TO 3 cases the following approximate values apply:
1. dry, without insulatar 0.05 - 0.20 K/W
2. with thermal compound/without insulator 0.005 - 0.10 K/W
3. Aluminium oxide wafer with thermal compound 0.20 - 0.60 K/W
4. Mica wafer (0.05 mm thick) with thermal compound 0.40 - 0.90 K/W
RthK = thermal resistance of heatsink, which can be directly taken from the diagrams
RthGM = sum of RthG and RthM. For parallel connections of several transistors the value RthGM can be determined by the following equation:
Equation 3:
=
+
+ ... + 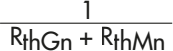
The result can be substituted into equation 1.
K = Kelvin, which is the standard measure of temperature differences, measured in °C, therefore 1°C = 1 K.
K/W = Kelvin per watt, the unit of thermal resistance.
Calculation examples:
1. A TO 3 power transistor with 60 watt rating has a maximum junction temperature of 180 °C and an internal resistance of 0.6 K/W at an ambient of 40 °C with aluminium oxide wafers.
What thermal resistance is required for the heatsink?
given:
P = 60 W R thG = 0.6 K/W
θi = 180 °C - 20 °C =160 °C (for safety margin) RthM = 0.4 K/W (average value)
θu = 40 °C
find: RthK using equation 1 RthK = θi θu − (RthG + RthM) =
− (0.6 K/W + 0.4 K/W) = 1,0 K/W
1.3 Same conditions as above but for three devices with equally distributed power ratings.
solution use equation 1 and equation 3
=
+
+
=
W/K RthGM ges. =
K/W = 0.33 K/W
substitute into Equation 1 gives: RthK =
_ 0.33 K/W = 1.67 K/W
With these values determined, the tabulation on page A 13 - 17 can be used to give a choice of possible heatsink profiles. Then by examination of the drawings and curves the final choice can be made.
3. A transistor with power rating of 50 W and internal thermal resistance of 0.5 K/W has a case temperature of 40 °C. What is the actual value of junction temperature?
given:
P = 50 W R thG = 0.5 K/W θG = 40 °C
find: θiusing equation 2
θi = θG+ (P • RthG) θi = 40 °C + (50 W • 0.5 K/W) = 65 °C
Thermal resistances of any profiles with forced convection
RthKf ≈ a • RthK
RthKf = thermal resistance with forced convection
RthK = thermal resistance with natural convection
a = factor of proportion
2.Performance, service life and reliability of electronic semiconductor devices are significantly determined by the thermal load to which the devices are exposed. An exceeding of the maximum operating temperature leads to malfunctions. An exceeding of the permissible junction temperature leads to a destruction of the semiconductor. To make it worse there is an advancing trend in the semiconductor industry for continuous increasing integration- and power densities of electronic devices. For the solution of thermal problems the first question is which kind of heat dissipation has to be considered. For this there are different processes available: by means of free convection (passive) with different heatsink solutions, by means of forced convection (active with help of fans, cooling aggregates) or by means of fluid media (fluid cooling).
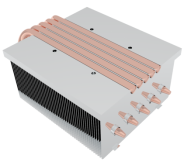
However, electronic devices and systems have many different boundary and installation conditions. Therefore the choice of the optimum thermal management is often difficult. There are surely possibilities to find the right heat dissipation concept by using the thermal resistance for calculations or by testing and verifying prototypes directly in the application, but nowadays customer specified mechanical adjust - ments are requested and demanded more than ever. Small mechanical post-machinings, such as additio- nal integrated threads or drilling can be considered in the calculation with safety reserves in the tempera- ture of the thermal resistance, but extensive modifi-cations demand a repeated inspection of the thermal circumstances.
Considered factors in the thermal simulation
With KINGKA thermal simulation, the necessary characteristics of the cooling concept can be accurately determined. Based on physical concepts such as mass, energy and impulse, the software specifically considers the thermal requirements of natural or forced convection. At the same time, the system dissipates heat via the fluid. In addition, thermal simulation calculates physical effects such as thermal radiation and turbulence. The radiation factors of different surfaces also play a role.
KINGKA will be happy to advise you in detail about the theme thermal simulation. Our experts are at your disposal for all technical advice.
2.2 Role in Semiconductor Industry
Heat sinks play a vital role in maintaining junction temperatures within safe limits, preventing thermal runaway, and ensuring stable operation. They are crucial for protecting CPUs, GPUs, power semiconductors (IGBTs, MOSFETs), and other heat-sensitive components within integrated circuits and electronic assemblies.
2.3 Key Areas of Application
· High-Performance Computing (HPC): Essential for cooling processors in supercomputers and data centers.
· Automotive Electronics: Ensures reliability of electric vehicle inverters, ADAS systems, and infotainment units.
· Telecommunications: Maintains the performance of base stations and routers under heavy load.
3. Conclusion
Heat sinks are fundamental to the semiconductor industry's ability to manage the relentless increase in heat generation. Their design and manufacturing technologies continue to evolve, addressing the demands of emerging applications while paving the way for smarter, more sustainable cooling solutions. As the industry pushes the boundaries of performance and integration, the role of effective thermal management will only grow in importance.